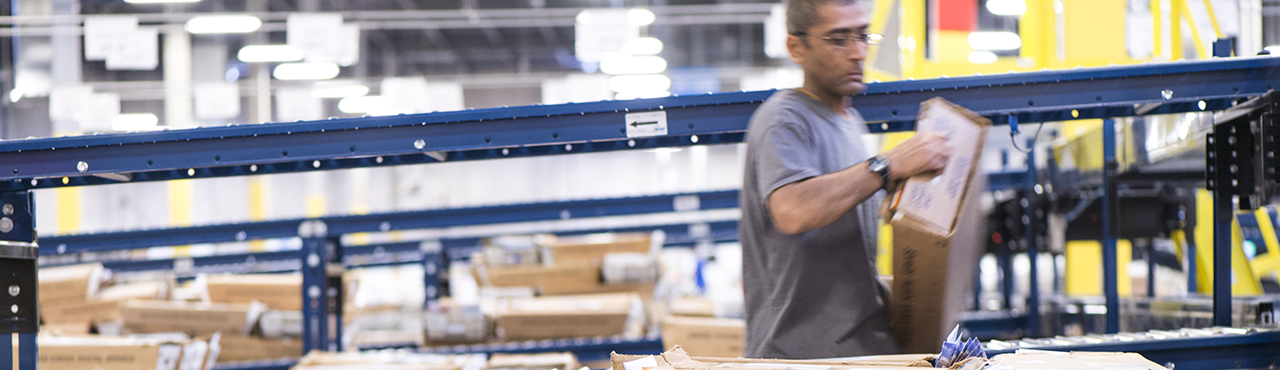
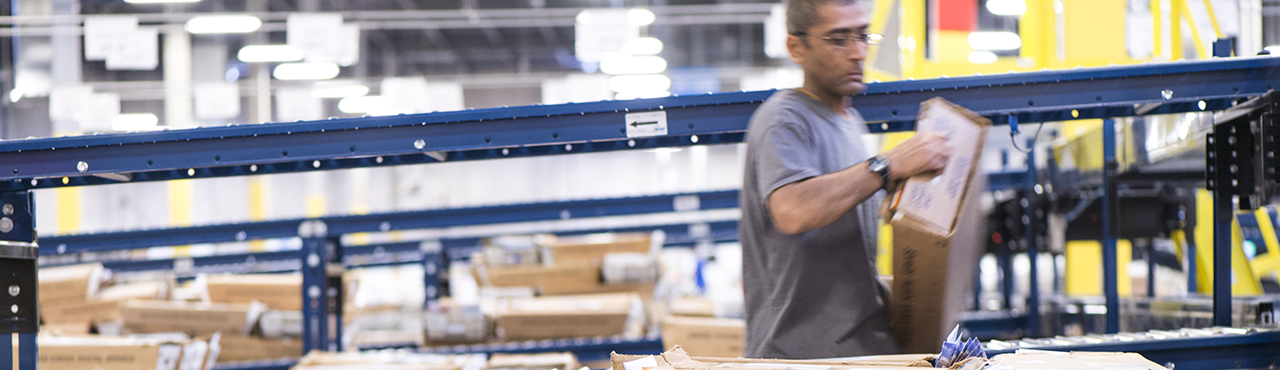
Smart, Simple Shipping & Mailing Solutions, Expert Mail room solutions | Pitney Bowes
How to improve your mail and shipping operations
Achieve a “world-class” competitive advantage in your workflows
Declining mail volumes, rising carrier rates, new compliance requirements and the constant drumbeat for innovation are putting more pressure on both mailing and shipping service providers and in-house operations to do more with less. Achieving operational excellence requires an intense focus on productivity, which can decrease expenses while increasing quality and value for customers.
“Printers and mailers must learn to adapt to changes in mail and application profiles, handling and adjusting multiple disparate projects,” says Richard Smith, head of Client Success Services at Pitney Bowes. “They must meet or exceed the service level agreements to which they’ve committed and improve their performance on compliance — but also be agile enough to respond to changing client needs.”
World-class operational excellence starts with determining the key performance indicators (KPIs) that are most appropriate for your operation. “These KPIs are typically aligned to quality, time and cost and are measured against desired outcomes and industry best practices,” Smith adds. “Using enhanced analytics, it’s possible to take a specific indicator — total cost per piece, cycle time, defects and more — and measure and compare the performance of sites within an enterprise and an enterprise within an industry.”
A thorough operational assessment can help you identify and eliminate bottlenecks and implement improvements across the workflow, optimising job set-up time, capacity management and job scheduling. It can also help you identify costs — in materials, labour and equipment — and connect them with processes in your production environment.
For example, are you measuring the cost of returned or delayed mail or parcels in terms of postage and labour, or for the more profound impact on customer relationships? How could investments in equipment or software to improve address quality reduce these costs, and what is the payback period? What about the cost of choosing the wrong carrier, the need to bring in additional labour during peak periods and how to address these issues?
“Productivity is at the core of optimised operations and production excellence,” Smith says. “Mail manufacturing productivity is about achieving consistent repeatable results and maintaining a disciplined mind-set focused on continuous improvement. Fortunately, evolving technology is giving managers greater insight into performance across the production environment.”
Room for improvement
Achieving operational excellence requires an intimate knowledge of your existing processes: who sends or receives items, when and how, and how volumes peak and ebb over time. It also requires an understanding of your organisation or client’s unique priorities: reducing costs, improving cash flow, maintaining compliance and more.
There’s little room for error. Is your production floor designed for maximum efficiency? What about the flow of mailing and shipping-related information within your organisation — and between your organisation and its partners and customers? Here are just a few factors to consider when examining your operations:
- Integration Examine the production space. Could separate tasks be combined into a single production line to improve productivity and space utilisation?
- Design Are the elements of your production space — equipment, furniture and more — situated and designed to ensure efficient processing and staff productivity?
- Centralisation Should you consider centralising (or decentralising) your mailing operations or output management
- Motivation Are your staff members properly trained and motivated to do their jobs? Do they have a clear understanding of expectations and goals? Do they feel valued?
- Visibility Is information siloed across your organisation, hindering your ability to assess costs and carrier performance and create more accountable procedures
- Education Are employees (or clients) creating challenges through late drop-offs, improper service requests or other preventable actions?
The role of technology
The proper use of technology in a printing, mailing or shipping operation will impact your business far beyond the confines of the mailroom. Consider the following advances:
- Automation While the all-manual mail shop is largely a thing of the past, sophisticated automation does more than speed up processing and save labour costs. It also improves accuracy and precision, which helps to ensure regulatory compliance, prevent customer service problems and allow for more targeted messaging.
- Industrial Internet Through the use of big-data-driven analytics and intelligent decision-making, the Industrial Internet — which refers to the integration of complex machinery, sensors and software — transforms the way production assets communicate with the enterprise. New solutions include predictive indicators to prevent service problems and better job scheduling and capacity planning tools.
- Lower-Cost Inkjet One relatively recent technology — the inkjet system — has transformed print operations. These high-speed, continuous-feed systems enable 100 percent variable data colour printing, eliminating the need for pre-printed forms and allowing consolidation of multiple functions into one machine. Newer, lower-cost systems are now making inkjet cost-effective even for mid-range volumes.
“A sustained drive to operational excellence requires executive buy-in, focused planning and follow-through,” Smith says. “But even minor operational improvements can increase your production yields and improve financial performance.”
We encourage you to learn how a technology partnership with Pitney Bowes helped a leading transactional print provider achieve new levels of operational excellence and land a 10-year deal.
© Pitney Bowes 2015. All rights reserved.