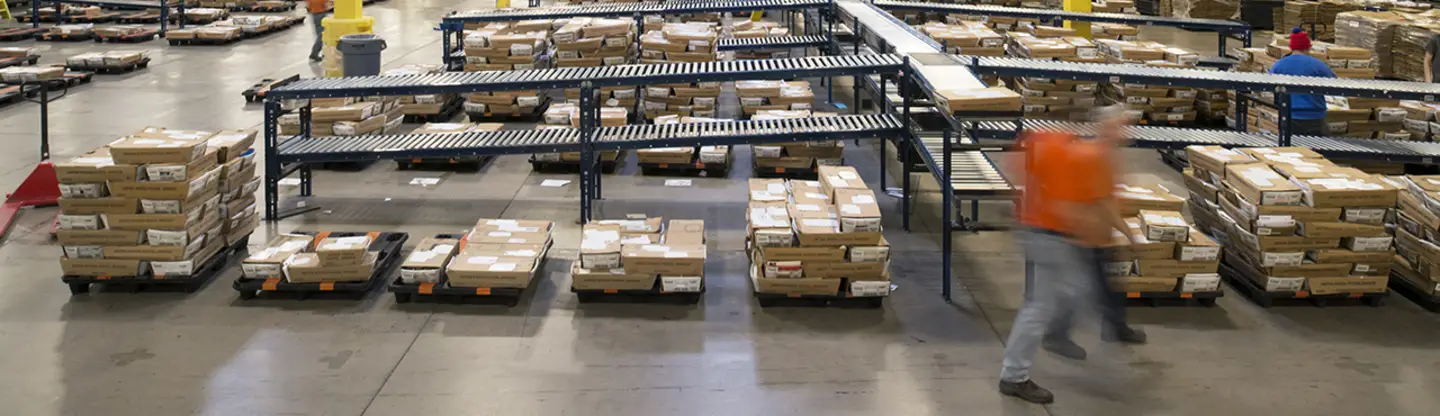
How warehouse operations are speeding to “quick delivery”
When people decide to buy something in the B2B or B2C world, they expect to be able to track it from the moment they provide their payment information to when the order is in their hands. Warehouse technology that supports this process — and the new omni-channel world of ordering — involves all kinds of complexities in the back-end, from inventory visibility to warehouse automation and inventory coordination. Let’s look at each of these to see what’s changing to meet the new demands of shipping orders.
Real-time inventory visibility
If a customer orders three different items from the same retailer, the items may come from three different places — say, one retail store and two distribution centers. In order to achieve a promised two-day delivery, companies need to have a granular view around both inventory location and distance from consumer.
“There is nothing worse than to have someone place an order and only then determine that the inventory isn’t close enough to a distribution hub to deliver it within the promised time,” explains Chris Petersen, president of the consultancy Integrated Marketing Solutions. “To ensure you can deliver the products in time, you need perpetual real-time inventory.”
Achieving real-time inventory requires real-time visibility into all the systems necessary to fulfill the order: online ordering, distributed order management, transportation management and warehouse management.
Retailers need to know not only which distribution center has the item, but also what aisle or location the item is in. “To achieve this level of accuracy, retailers need embedded GPS/RFID capabilities, which allow products to be tracked as they move through the supply chain,” Petersen says.
Removing warehouse waste
Large retailers are using automated or semi-automated systems inside their distribution centers to speed order fulfillment. Automated technology can reduce human error and delays by such means as capturing the weight and dimensions of items to determine the most efficient way to pack them for shipment.
“If you’re implementing a quick delivery, you need to pick, pack and ship the product as quickly as is humanly possible,” says Marc Wulfraat, president of MWPVL International, a consultancy in supply chain logistics and distribution.
Or actually even faster than is humanly possible.
In the past, one large ecommerce company had workers go through the aisles of its sprawling warehouses to find the items for a shipment. Now that task is handled by robots, which determine the most efficient way to bring the items to the workers, who stay at their packing stations. The change has reduced the time needed to pack an order from 90 minutes to 15 minutes — a significant difference for products with ultra-short delivery timeframes.
The amount of automation needed will vary, depending on factors like the types and number of items a retailer carries. “If you are talking a million-square-foot distribution center with 300 people, everything should be automated,” Wulfraat explains. “If your warehouse is a 10,000-square-foot garage, it may be a different matter.”
Moving it the last mile
Warehouse automation is becoming even more crucial as companies introduce promises of ever-faster delivery. For instance, the growing trend of same-day delivery demands both heightened efficiency in the warehouse and in the “last mile,” where products are put into the customer’s hands. Retailers are experimenting with a variety of ways to carry products over the last mile to the customer’s home, from traditional carriers to new regional carriers to ride-sharing services.
“When you have two hours to prepare your transportation plan, you’re really pressed to reduce drive time and the distance to ship out products in the most logical way,” Wulfraat says. “As orders come in real time, you need systems that can grab ZIP codes and organize them in clusters as close to the final cutoff time as possible,” giving your workers the maximum amount of time to process and deliver.
Mapping technology allows retailers to simulate how much time is required to perform each outbound route and minimize travel time. They can use updated travel information to determine if routes should be changed and keep tabs on the location of drivers to identify issues that may delay arrival times.
Moving forward, customers in both the B2B and B2C world will expect a wide range of choices regarding delivery times. Modernization will be the key component to ensure that the shipping function becomes a competitive advantage and raises customer satisfaction.